Chillers
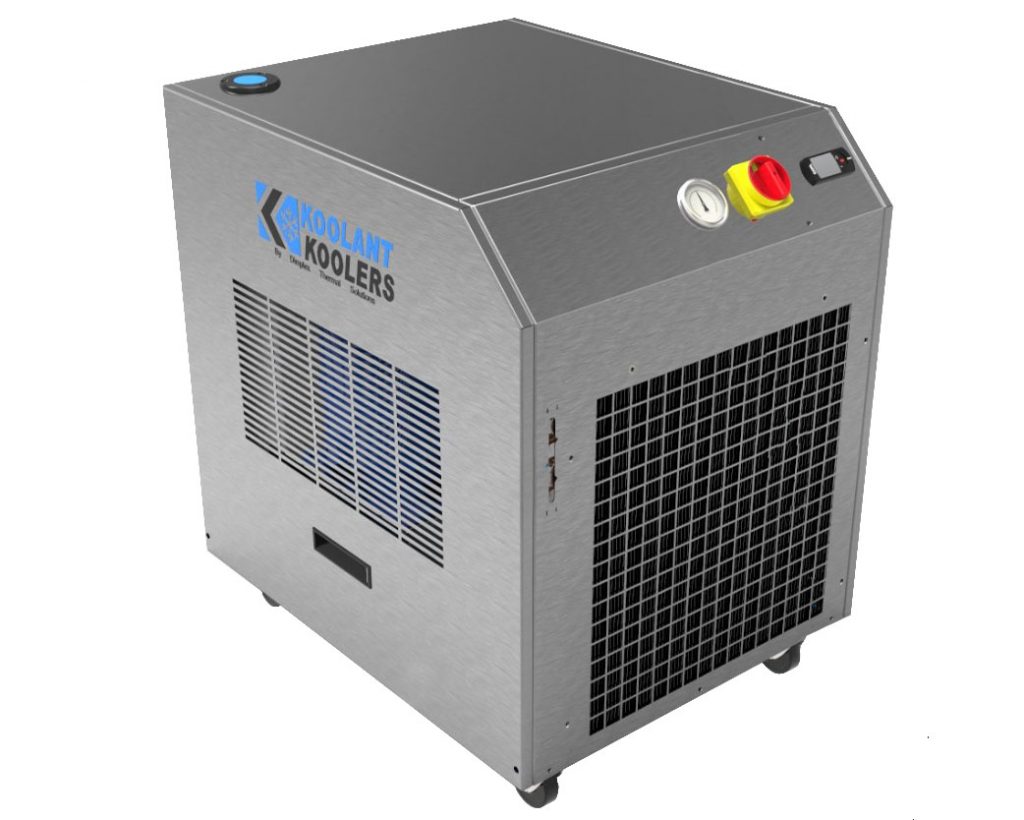
Chillers vs. Water Recirculators
What’s the difference between a chiller and a water recirculator? The major difference between the two is whether or not the unit contains a refrigerant.
An actual CHILLER will have a compressor and a pump to actively remove heat from the liquid flowing through it, using a refrigerant (much the same way a refrigerator or a drinking fountain works).
A WATER RECIRCULATOR does just that; it recirculates coolant through a radiator (much like the radiator in your car). It passively cools liquid by using a heat exchanger and cooling fins.
Do I need a chiller or a recirculator?
There is no simple rule to determine whether you need a chiller or a recirculator. If you are welding in high production, welding aluminum, or other important or exotic applications, a chiller is the clear choice. If the production rate is low, or the machine is used infrequently, a recirculator is probably fine. Please contact us for details.
Chiller Sizing
A general rule for sizing a chiller is that, for every 100KVA of welder, you should have about a 1-ton chiller. For example, if you want to cool 4 welders that are 100KVA each, you will need a 4-ton chiller. If you want to cool a 300KVA machine, you will need a 3-ton chiller. See below for further sizing details.
BTU calculations, with duty cycle taken into account
If you want a more accurate method for determining your chiller or recirculator size, you can use the formulas below.
To calculate BTU’s per hour of a resistance welder:
Resistance Welding: BTU/hr = (welder KVA) * (duty cycle) * (.85) * (.6) * 3415 BTU/hr
Resistance Welding: BTU/hr = (Welder KVA) * (Duty Cycle) * (Eff Power Supply) * (Eff Heat Collection) * 3415
Eff. Power Supply: the % of power out to power input; typically 85%
Eff. Heat Collection: the % of heat absorbed by the chilling water; Varies 50%-75% est
To calculate duty cycle:
(weld time on) / (elapsed time) = duty cycle
Example:
Say you are averaging 4 welds per minute on a 100KVA welder with a weld time of 15 cycles (250ms).
duty cycle = [(number of welds) x (weld time, in cycles)] / 3600
duty cycle = [4 * 15] / 3600 = 0.016667 = 1.67%
BTU/hr = 100 * 0.8 * 0.016667 *0.6 * 3415 = 2732 BTU/hr
Image Gallery

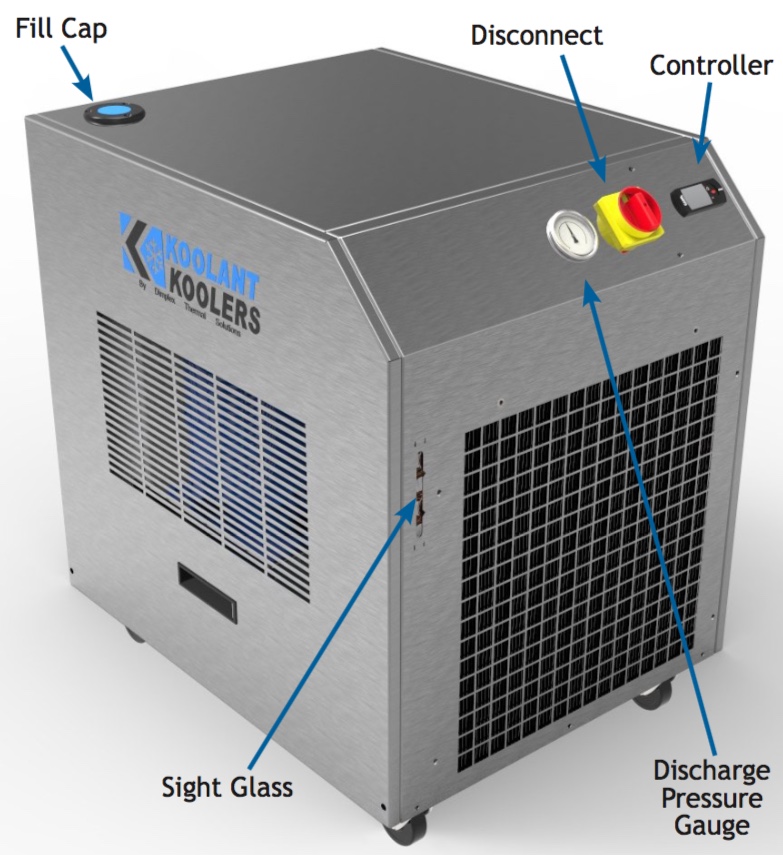
J-Series Chillers
1/8th ton
1/2 ton
1 ton
1-1/2 ton
2 ton

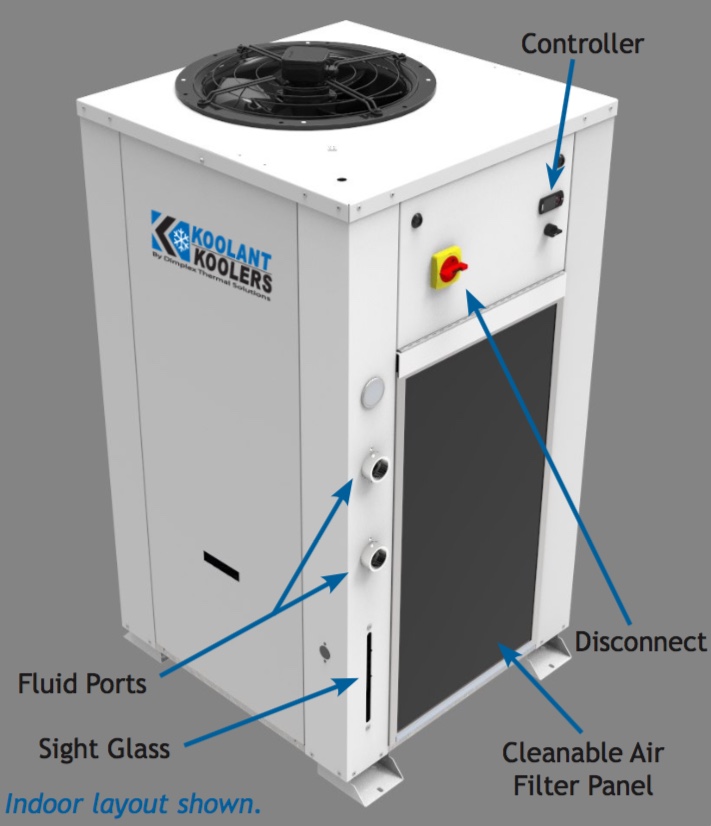
S-Series Chillers
3 ton
5 ton

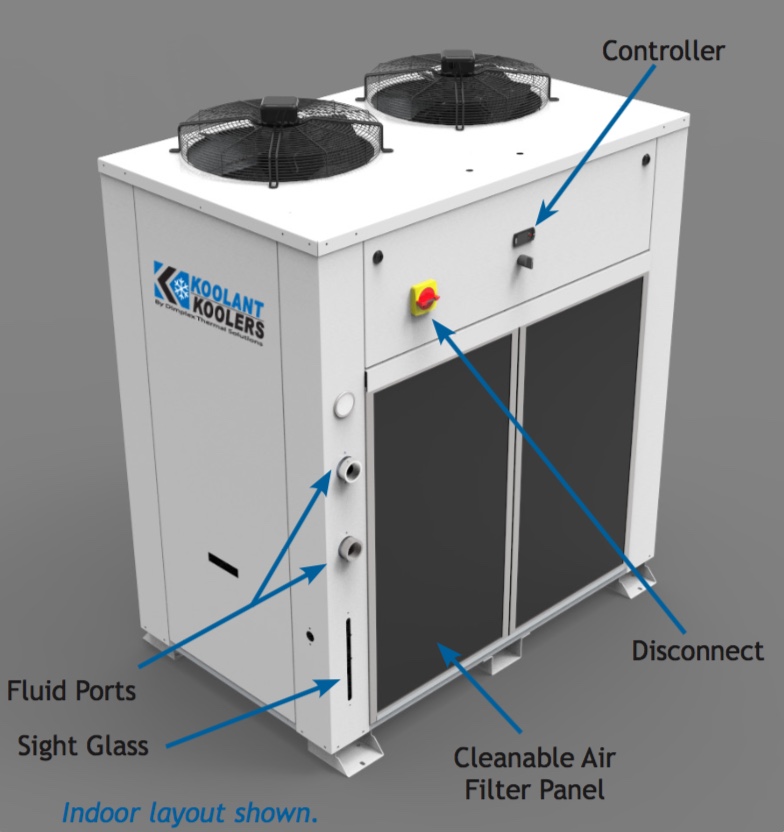
S-Series Chillers
7.5 ton
10 ton

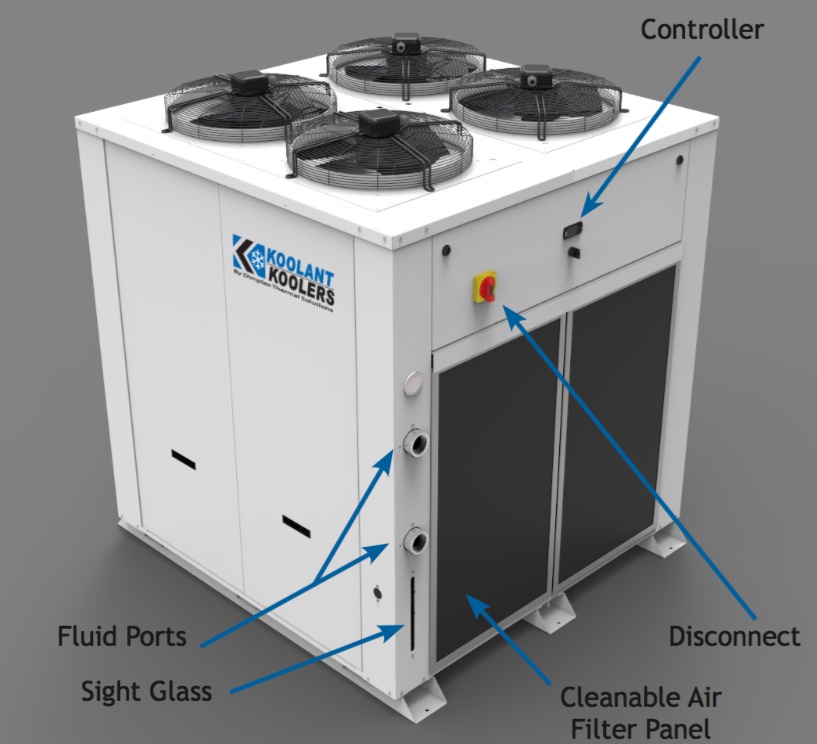
S-Series Chillers
15 ton
20 ton